Vessel Upgrade
There’s always room for improvement! This upgrade was developed based on market needs and client requests. This design was needed to speed up the evaporation process and reduce the total time that it takes to complete an extraction cycle. Time is money. The quicker the extraction process, the more profitable it is for clients.

12" Evaporator Sectional - Clients were requesting a way to increase the evaporation of the solvent and speed up the recovery process of extraction.
Adding a coil to the evaporator increases the evaporation potential and makes the evaporator much more efficient.

Example of an existing coil in the market

A custom adapter was needed in order to accomplish the goal of adding the existing coil to the evaporator.
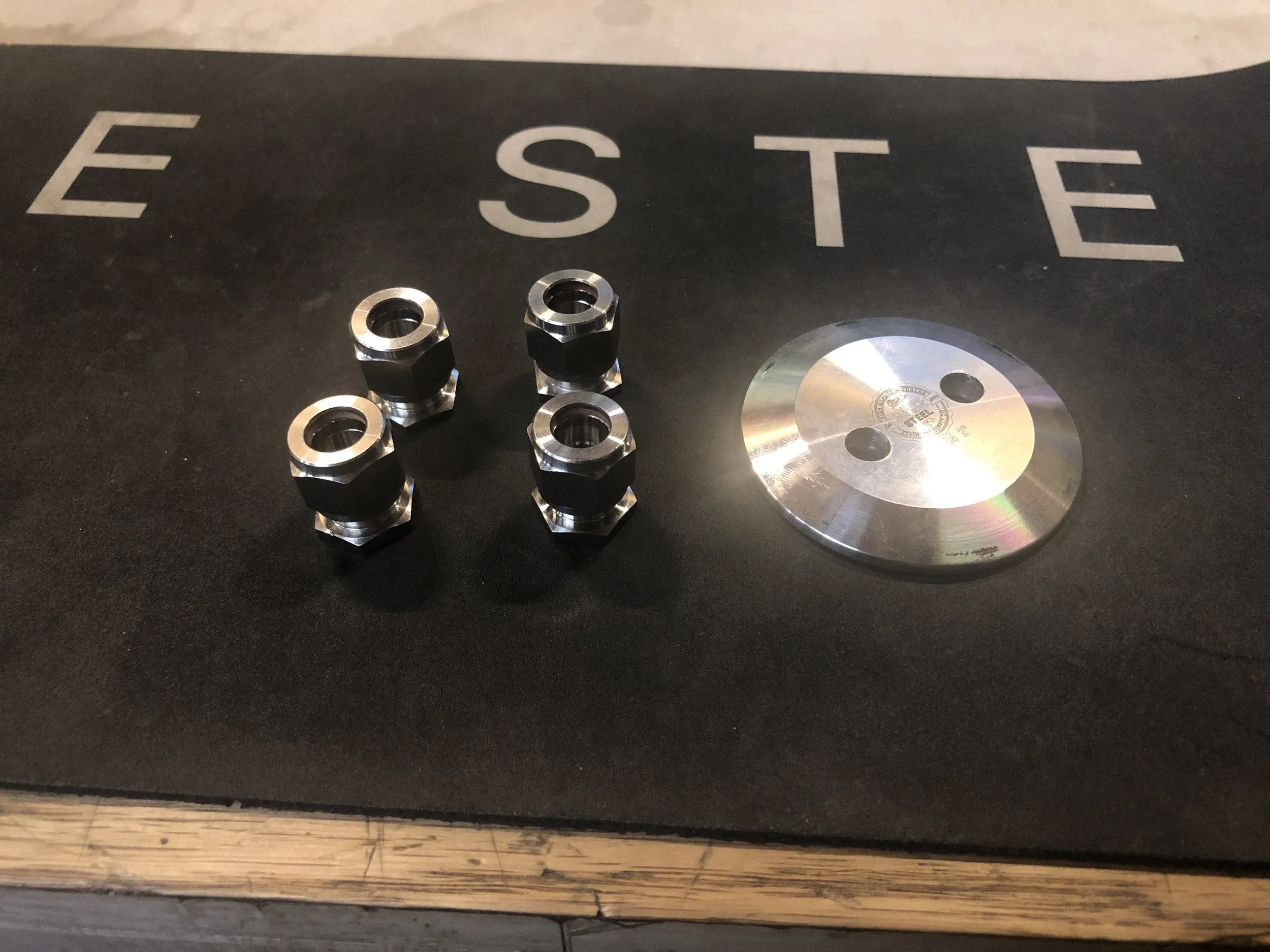
Here is the prototype of the custom adapter. I drilled holes in a 2" tri-clamp flat cap using a drill press. Then I cut 2x 3/8" compression union fittings in half on a band saw. Then I welded the fittings to the flat cap using a TIG welder.
Here is the custom adapter after it was welded and put under pressure.
The size of the evaporator was long enough to support two coils daisy-chained to each other. Connecting two coils to each other further increases the vessel's evaporation potential.
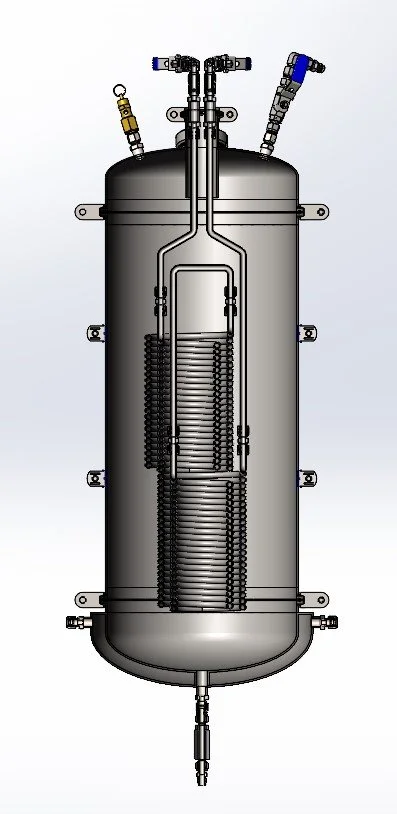
Precise tubing bends were needed in order to connect the two coils to each other and also to connect to the custom adapter at the top of the vessel.
Why was this design needed?
Increase the surface area contact for evaporation
Speed up evaporation
To adapt around the limitations of the lid
What design skills were used in this project?
Sketching from and referencing existing designs
3D sketching and creating custom planes
Volumetric calculations
Creating one and two coil configurations
Creating products that reference other parts
Sketching and modeling helix shapes
Mating components and assemblies
Render multiple views and sectionals
Sourcing existing products suitable for the design
Research of coils
Using whats available to make a product